How to Perform a Safety Inspection at Work to Avoid Accidents
abril 16, 2025 | by Safety For Job Team
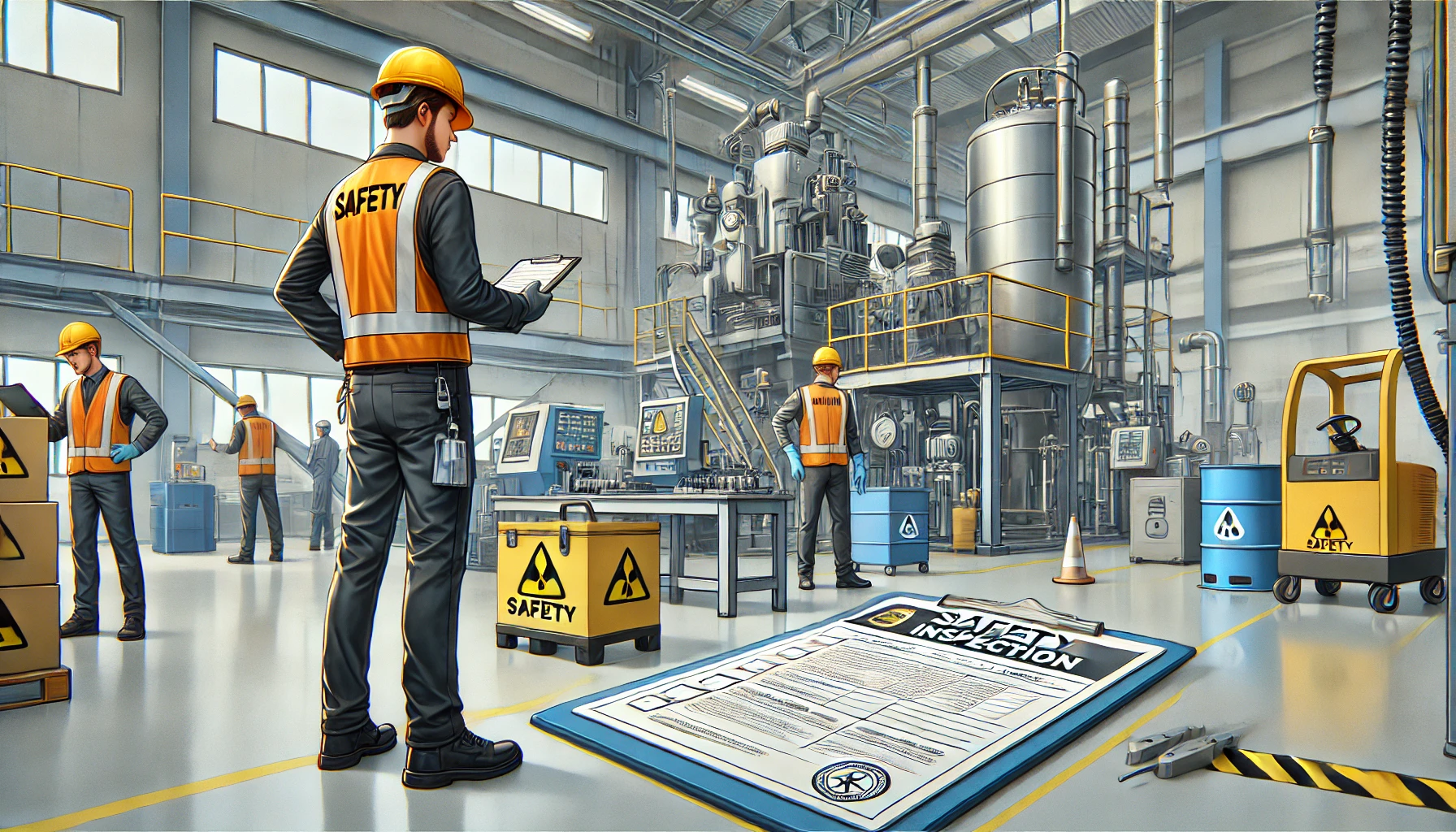
Safety at work is one of the top concerns in any workplace, especially in operational, industrial, or high-risk environments. Safety inspections are key tools to prevent accidents, allowing you to spot potential hazards before they turn into real problems. In this article, you’ll learn how to conduct an effective inspection, why it’s essential for workplace safety, and how to take corrective actions based on what you find.
What is a Safety Inspection?
A safety inspection is a systematic check-up of the workplace, equipment, processes, and behaviors, aiming to identify unsafe conditions or actions that could lead to accidents or occupational diseases. It’s a preventive task that promotes a safer work environment for everyone involved.
You can conduct safety inspections regularly (daily, weekly, monthly) or on an exceptional basis (after incidents, process changes, new equipment installation, etc.).
Safety Toolbox Talk: Welding — MSDs Ergonomics
Why is Safety Inspection So Important?
The importance of safety inspections goes beyond just checking off a box. A well-conducted inspection:
- Spots risks before they cause accidents
- Cuts down on costs from absences and compensations
- Boosts the company’s image with employees and regulators
- Strengthens the safety culture at work
- Serves as the foundation for training, like the DDS (Daily Safety Dialog)
Plus, regular inspections show that the company is committed to the health and safety of its employees, which positively impacts the workplace atmosphere and productivity.
Steps for a Good Safety Inspection
1. Planning the Inspection
Before heading out to inspect, make sure to define:
- Which area or department will be inspected?
- What regulations and standards should be considered?
- What’s the specific goal of the inspection?
- Who will participate (Safety Committee, technicians, managers, etc.)?
Having a customized safety checklist is essential. It should include items related to the physical environment, machinery, equipment, PPE use, signage, organization, and safe behaviors.
2. Conducting the Inspection
During the inspection, those in charge need to carefully observe every item on the checklist. Be sure to:
- Take notes and pictures of everything
- Talk to employees to understand daily practices and potential operational flaws
- Watch for behaviors, not just equipment (e.g., posture when handling tools, correct PPE use)
Avoid making judgments. The inspection should be educational and corrective, not punitive.
3. Identifying Risks and Non-Conformities
You might come across situations like:
- Damaged or misused equipment
- Exposed wiring
- Missing or incorrect safety signage
- Lack of training for critical tasks
- Improper posture from employees
Make sure to document each item in detail to make future evaluations easier.
4. Risk Classification
Once identified, risks should be classified by severity and the likelihood of occurrence. This way, corrective actions can be prioritized. Here’s one way to classify risks:
- Critical: Risk of a serious or fatal accident
- High: Significant risk of an accident leading to time off
- Moderate: Risk of a minor accident or occupational disease
- Low: Unlikely risk with no severe consequences
5. Creating and Monitoring the Action Plan
Based on your findings, create an action plan that includes:
- Problem description
- Corrective actions needed
- Person responsible
- Deadline for resolution
- Re-evaluation date
It’s crucial to follow up on these actions. There’s no point in identifying risks if they’re not eliminated or controlled.
6. Communicating the Results and DDS
The inspection results should be shared with all involved, especially the leaders of the inspected areas. A great practice is to use these findings as the basis for your next DDS (Daily Safety Dialog), raising awareness in a practical and direct way.
For instance, if incorrect PPE use was spotted during the inspection, the next DDS could focus on the importance of using protective equipment properly.
Safety Toolbox Talk: Welding — MSDs Ergonomics
Tips to Make the Inspection Even More Efficient
- Involve employees: Encourage active participation by showing that safety is everyone’s responsibility.
- Use technology: Inspection apps can speed up the process, generate automatic reports, and make it easier to track actions.
- Train inspectors: Inspectors should understand the risks of the tasks they’re inspecting and be technically knowledgeable.
- Update the safety checklist regularly: Adjust it as the operation changes.
- Create a history of inspections: This helps identify recurring patterns or issues.
Conclusion – Safety Inspections
Safety inspections are powerful allies in preventing accidents. When done with care, planning, and commitment, they become a strategic tool to protect employees’ physical integrity and ensure the safe continuation of operations.
Remember: workplace safety isn’t a cost, it’s an investment. Simple actions like using a safety checklist and reinforcing safety daily through DDS make a huge difference in building a safe and productive environment.
Estimated reading time: 5 minutos
RELATED POSTS
View all